Do you know it? There are problems in production and the different departments involved, such as production, quality and development, are not getting the issue solved. In addition to the personal distance of the people involved, there is often also the physical distance. The consequence: responsibility is passed on in the circle of departments. I have a real-life example of this: an international supplier of composite automotive and aerospace components. I would like to explain the background and possible solutions in this article.
Waste is produced during processing – but why?
I was asked to find out why, during the finishing of an aircraft bulkhead, a milling cutter on the machining center occasionally came loose and came out of the holder by 2-3 mm. The consequence was that it sat too deep in the subsequent machining and milled the pockets and recesses too deeply. The components could no longer be repaired and used and were therefore expensive scrap, which was attributed to production each time.
So I started in the quality department to get the necessary numbers, part numbers, incidents and reports. From this, I then derived my plans for process analysis and for identifying possible sources of error using the Turtle method.
Then I went to the responsible CAD/CAM designer to have a look at the processing program and a simulation of the processing. This was also done with regard to cutting speed, feed rate and infeed in comparison to the recommendation/data sheet of the milling cutter manufacturer.
Then the production started. Due to my background as an industrial mechanic, I naturally first inspected the condition of the tool chucks and the set-up procedure. At first glance, this seemed satisfactory. The subsequently machined partition wall also showed no abnormalities and was in order.
An observation brings a hint
The next morning a new incident occurred on another component. I now marked the cutter shank at the transition to the chuck with red tape. Then I watched the finishing of some parts to see when and where it came off. For some parts nothing happened at all. But then finally, the next day, you could hear the machining center on a part at a very specific point (see picture above), and it was asking for more. A look at the milling cutter confirmed this. A gap had appeared between the chuck and the red tape.
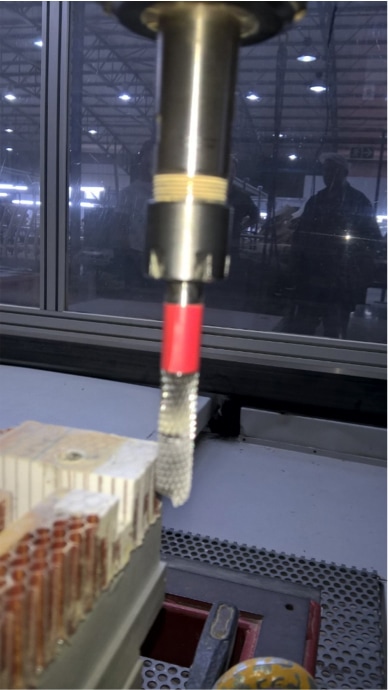
We stopped the processing immediately and found the solution to the puzzle. Due to different versions and different ways of fixing and connecting this partition wall, there was a fiberboard insert at this point of the composite sandwich for which the processing was designed. The solution was then simple. We searched all versions for deviations and adjusted the processing on the CAD/CAM version accordingly.
Good planning requires thinking along with all participants
It was very impressive to see that departments often only see themselves and their tasks and do not see the big picture. Often they also do not have the time and competence to deal with it. With my experience in the positions described above, I can support them as a trainer and “translator”.
Small note: The described example was in production in the company for over half a year. By avoiding the costs of one month’s scrap, my fee was paid.
Based on my experience in all kinds of areas and levels in a company, I can mediate and promote communication in such and similar cases. So if you also need a “departmental translator”, please contact me at +49 7161 988-4470 or at info@linge-composite.de