Mould making for composite components is a fundamental field that is absolutely crucial for the success of projects. In mould making, problems are solved before they arise – or, on the contrary, numerous problems arise that show up in later production phases and often cost the company dearly.
In the case I would like to present to you here, a company that had just entered the field of composites asked me for support. Difficulties had promptly arisen during the mould construction of the first project and they called me in to speedily resolve them.
In mould making, materials must harmonise
Already in the first conversation it turned out that the material currently used in mould making did not at all correspond to the wishes for the later production of parts. The reason was the necessary glass transition temperature of the resin for the planned manufacturing process. The tool, i.e. the mould, was not constructively suitable for providing this temperature.
As a test, a new mould was made from a different material, but this also caused problems. In this case, it was a chemical reaction of the gelcoat of the tool with a material used at the master pattern.
The surest way to success is controlled experimentation
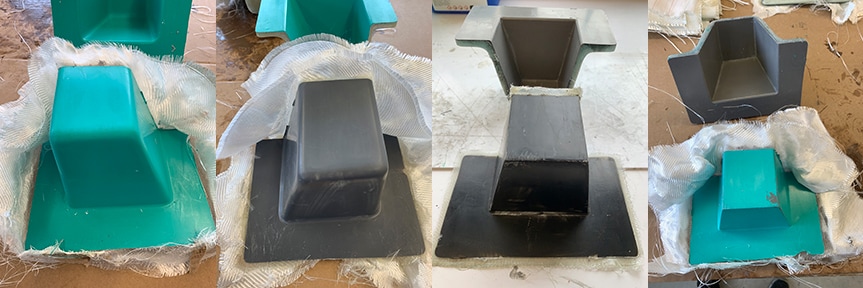
Different material pairings as well as resin systems were now systematically tested in order to have greater flexibility in the subsequent production of parts. Different release agents were also checked for their compatibility, and the corresponding tempering cycles were analysed.
The result was a beautiful tool, which can be seen in the picture below directly after demoulding. The edges still have to be deburred and the surface gets a cleaning and polishing. After that, production can reliably begin.
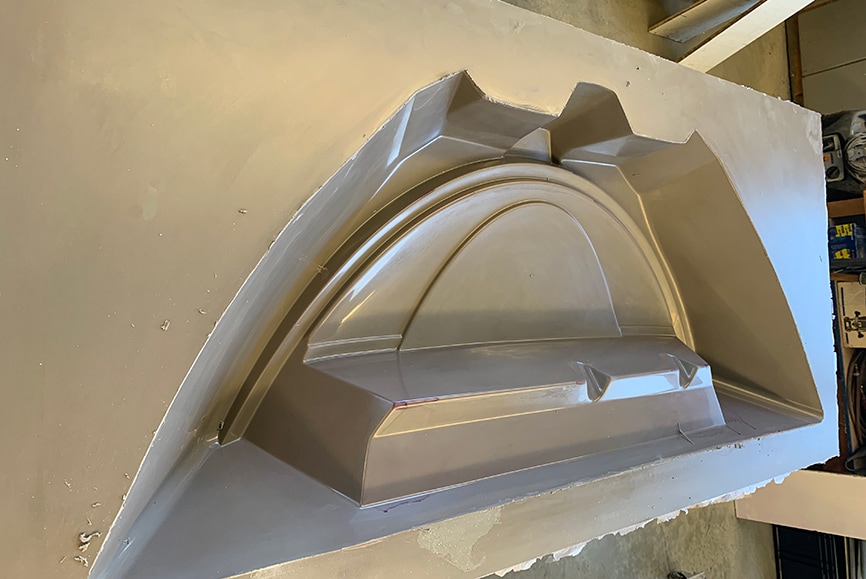
Where do you have a need for optimisation that I can support you with?
Good planning pays off several times over in the development of carbon composite components. Let us discuss your project early on! You can reach me at +49 7161 988-4470 or info@linge-composite.de